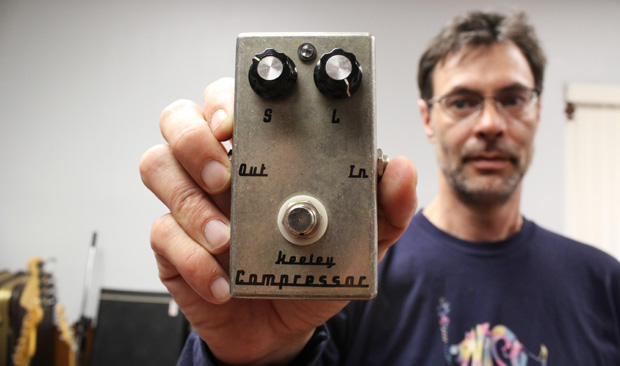
Robert Keeley
Joe Wertz / NPR StateImpact
Robert Keeley
Joe Wertz / NPR StateImpact
Joe Wertz / NPR StateImpact
Robert Keeley and the first-ever Keeley Compressor, the first and best-selling effect his company manufactures.
Jeans and rock band t-shirts are the uniform at Keeley Electronics, and almost every one of the 18 or so employees works with earbuds in — and an iPod nearby.
This doesn’t seem like a factory, but it is. And it’s growing and expanding in a state that’s been hemorrhaging manufacturing jobs.
Joe Wertz / NPR StateImpact
Technician Shaun Brown assembling the components of an effects pedal, which are all hand-wired.
Robert Keeley’s office is a waist-high sea of guitar amps.
Downstairs is flooded, too. He opens the door to one office space with caution. It’s wall-to-wall guitars, which are filed neatly in their cases.
“Everyone is surprised when I say I’m a manufacturer. ‘Really? In Edmond, Oklahoma?’,” Keeley says, recounting a puzzled tone he regularly hears.
The business began with a bad omen.
Keeley shipped out his first guitar effects pedal on Sept. 11, 2001.
The electrical engineer and guitarist got to the post office early, “before everything came apart,” and mailed a Keeley Compressor to his first customer. The eBay sales picked up, and a year later he decided not to return to his job at Vatterott College, where he taught tech students basic electronics.
“From there it was pure magic,” he says. “Every year the sales doubled.”
In 2004-2005, Keeley’s effects pedals were added to a catalog assembled by venerable guitar maker Fender, which distributes the publication of musical instruments to brick-and-mortar dealers throughout the country.
“Every mom-and-pop shop in America had a catalog with a Keeley Compressor in it,” Keeley says.
It didn’t stop with catalogs and local dealers. Musician’s Friend added his pedals to their roster of products, and Guitar Center started carrying Keeley’s pedals in some of its stores. Instrument dealers now comprise about 75 percent of his sales, Keeley says.
But Keeley Electronics really came alive in 2005.
Legendary English musician Peter Frampton has a signature sound defined, in part, by the “talk box,” an unmistakable effect he helped popularize in the mid-1970s.
The effect employs a tube, which allows a musician to use their mouth to change the frequency of a guitar or other instrument — to “talk” or sing through the instrument, in effect.
(Fast-forward to about :15 in the video to the right to hear it yourself.)
In 2000, Peter Frampton started selling his own version of the talk box. When Frampton started looking for a new company to take over manufacturing, he turned to Keeley, who he’d been trusting to repair his vintage effects.
After a show in Nashville, Frampton invited him up to his hotel room, Keeley says.
“The deal was kind of done on a handshake,” he says, and Keeley Electronics has been making Frampton’s signature “Framptone” talk box effect since 2005.
By 2008, Keeley Electronics reached $2.5 million in sales, growth led by their first and best-selling product — the Keeley Compressor — a guitar effect beloved by both amateur pickers and celebrity strummers like John Mayer, Pearl Jam and Dweezil Zappa.
Keeley’s company had caught fire. In January 2009, it caught fire — literally — and the full force of the recession nearly smoldered his business.
The layoffs started that year, Keeley said. More than a dozen employees were let go, cutting his full-time staff by more than half.
“The economy was really tanking then,” he says. “It was really sad. It wasn’t anything they were doing wrong, I just couldn’t afford them.”
Keeley wasn’t alone.
Joe Wertz / NPR StateImpact
Crystal Gilles attaches switches and input jacks to a case that will house an effects pedal.
Oklahoma lost more than 15,000 non-farm jobs from 2009-2010, data from the state Department of Commerce show. Manufacturing bore the brunt of those losses here as it did throughout the country. About 6,200 — or 40 percent — of those losses were manufacturing jobs, the data show.
Recently, the news is better. The number of manufacturing jobs increased 5.9 percent from January 2011 to January 2012, which Commerce officials say added about 7,400 people to the Oklahoma workforce.
Business has picked up at Keeley.
Keeley Electronics is growing and hiring — and Kelley has re-hired many of the same workers he was forced to layoff during the worst of the recession.
Keeley effects are wired and assembled by hand in a small, two-story unit next to a college dorm in an Edmond office park. Men — and a surprising amount of women — solder each and every resistor and component to bright green circuit boards.
Joe Wertz / NPR StateImpact
Matthew Adams uses a drill to tightly wind wire that will be used to connect electronic components.
Every screw, bezel and washer is hand-tightened. Effects pedals — often called stompboxes — are foot-operated, and the result of the hand-assembly process is a sturdy metal brick that protects delicate electronic audio components.
Hand-building the effects pedals also gives the technicians a keen understanding of how to repair a customer’s unit. Keeley also does brisk business repairing vintage effects and modifying other manufacturer’s pedals, which customers send in for customization.
The current bottom line for Keeley Electronics: roughly 1,000 units a month.
And Keeley’s pedals aren’t cheap.
“They are expensive,” he admits. “The components and craftsmanship are just part of it,” he says. Doing repairs is costly and time-consuming, too, he says. And then there are your workers.
“It takes a lot of money to pay people right,” Keeley says. “It takes a lot to be in business in America.”